Sustainability
EXEDY Group's Sustainability Activities
Global Human Resources Development
Human Resources Development Program
At the EXEDY Group, we put effort in the development of new graduates. Since FY2016, we set up individual "ten-year training plans" for each new graduate, and carry out training based this plan. Once every four months, Human Resources representatives hold one-on-one interviews and discuss work and the workplace environment. Each department prepares detailed yearly plans on which we base the education so employees acquire technologies and know-how in a timely way. We also carry out strategic rotation including overseas training. This system allows our employees to gain valuable experience at a young age.
Stratisfied Education and Training Programs
Aiming to develop human resources who will contribute to the sustainable growth and evolution of the EXEDY Group, we have many educational programs in palce that seamlessly draw and execute the future image and growth of employees according to each level, age group, and purpose, as shown in the figure below.
In addition to our in-house courses, we provide 141 correspondence courses as well. The company covers 50% of the tuition fee for employees who complete a course.
We also offer courses related to manufacturing, and a wide variety of courses such as management and business skills, languages and OA skills.
GETS Lectures
GETS (Global EXEDY Technical School) was established in 2012 to support the employees trying to learn on their own initiative. Here we mainly carry out stratified education and specialized manufacturing training. In this specialized manufacturing training, in addition to practical basic skills and knowledge, we teach skills that can be used in the workplace, in levels ranging from basic to expert. Rather than learning while seated at a desk, we incorporate a lot of education where employees get to master skills by practicing. We hand down technology taking advantage of the experience of in-house and OB lecturers. Some courses are attended by people outside our company to learn the basics of manufacturing.
Global Management Training
The EXEDY Group, with bases all over the world, carries out management training to strengthen the management of overseas production bases and sales companies. The EXEDY WAY, which is the core of our company, embodies our values and way of thinking and leads the way to evolution globally. As managers at the various locations share this way of thinking, we are able to achieve further development.
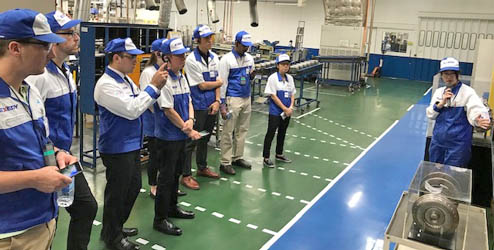
Plant tour at EXEDY HQ
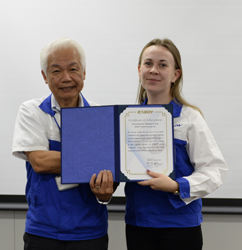
Participants receive a certificate of completion
Top Seminars
Since 2012 we have been inviting well-known individuals and people from our top management to EXEDY Headquarters to hold lectures. Until 2019, we held a total of 25 lectures. Through these lectures our employees learn about different ideas and perspectives. We hope this encourages them to grow, while keeping a broad perspective, and that they will incorporate this in their daily work.
QC Circle Activities
There are 300 active QC circles at EXEDY Corporation and worldwide there are around 1,100 circles. While employees grow through these activities solving work-related problems, we revitalize communication at the workplace. In the course of these activities, employees learn the problem-solving procedure that is the basis of quality, as well as nurture leadership and membership skills and improve field capabilities. In addition, we organize domestic and global QC Circle competitions to stimulate QC activities throughout the company while increasing the sense of unity and raising awareness towards improvement activities in the EXEDY Group.
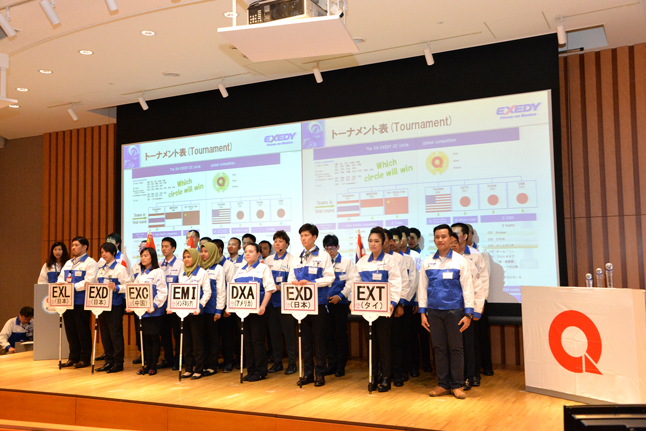
Elite circles that won domestic and international qualifications get to participate in the yearly Global QC Tournament.
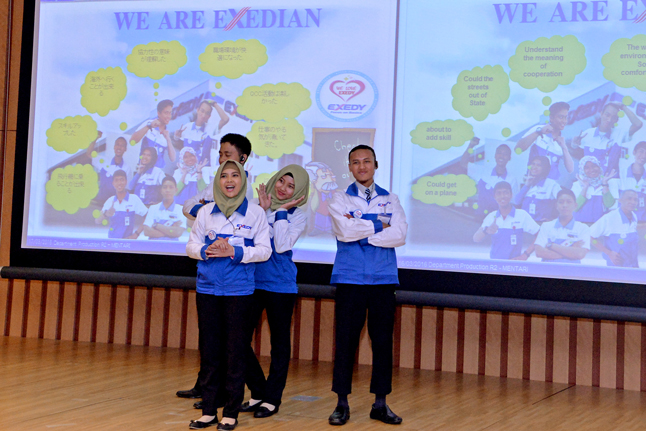
A creative and entertaining presentation by an overseas QC Circle
The best QC circles at the EXEDY tournament will participate in the various external QC Circle Conferences. Below we listed the major awards received by EXEDY’s QC circles.
QC Circle Convention Achievements (excerpt)
— QC Circle Headquarters / Union of Japanese Scientists and Engineers —
- Event
- The 6th Clerical, Sales and Service Section (Including Medical and Welfare)
Nationwide QC Circle Conference (Small-group Activities) - Date
- June 14, 2013
- Result
- Director’s Award Gold Prize
- Circle Name
- The Problem Solver Experts (Global Strategy Headquarters)
- Event
- The 46th Nationwide QC Circle Conference (Small-group Activities)
- Date
- November 29, 2016
- Result
- Director’s Award Silver Prize
- Circle Name
- Material Technology (Development Headquarters)
- Event
- The 10th Clerical, Sales and Service Section (Including Medical and Welfare)
Nationwide QC Circle Conference (Small-group Activities) - Date
- June 9, 2017
- Result
- Director’s Award Gold Prize
- Circle Name
- Fruit Nodoame (Purchasing Headquarters)
- Event
- The 48th Nationwide QC Circle Conference (Small-group Activities)
- Date
- November 27, 2018
- Result
- Director's Award Silver Prize
- Circle Name
- CAMCAM (Production Engineering Plant)
- Event
- The 12th Clerical, Sales and Service Section (Including Medical and Welfare)
Nationwide QC Circle Conference (Small-group Activities) - Date
- June 7, 2019
- Result
- Director's Award Silver Prize
- Circle Name
- Shushu Circle (AT Quality Control Department)
— QC Circle Kinki Regional Chapter —
- Event
- The 5981th QC Circle Kinki Regional Chapter Hyogo Area Convention
- Date
- November 17, 2017
- Result
- Regional Chapter Director’s Award
- Circle Name
- Right Now (Information Systems Department)
- Event
- The 16th QC Circle Champions Tournament in Osaka
- Date
- January 18, 2018
- Result
- Governor's Prize
- Circle Name
- CAMCAM (Production Engineering Plant)
- Event
- The 6104h QC Circle Tokai Regional Chapter Exchange Convention
- Date
- February 14, 2019
- Result
- Director's Award Gold Prize
- Circle Name
- Shushu Circle (AT Quality Control Department)
The Fruit Nodoame Circle (Purchasing Headquarters) was awarded the Director’s Award Gold Prize on June 09, 2017 at the Nationwide QC Circle Conference
Improving Technical Skills
In order to improve the technological capabilities of our employees, we carry out various activities throughout the entire EXEDY Group. The EXEDY Olympics are held with the aim of increasing the motivation of employees involved in manufacturing. Various members of the EXEDY Group compete their skills in disciplines such as forklift, measurement skills, crane, insert change and die exchange.
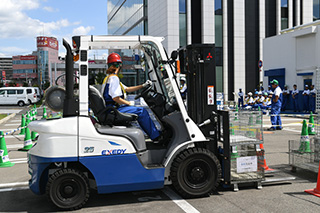
Forklift Olympic Event
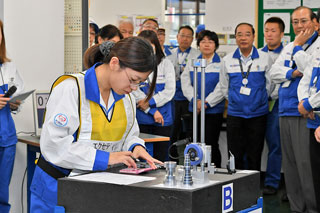
Measuring Skill Olympic Event